Recently, the upstream materials of PCB have been rising one after another, except that the international copper price has been breaking through 7000 US dollars and approaching 8, In addition to the $000 mark, the supply and demand of electronic grade glass fiber cloth and glass fiber yarn are also reversed. After the third quarter of 2020, there is a general increase of about 20%. This will naturally be an obvious cost pressure for CCL and PCB industry. However, the PCB industry frankly said that the main target of this impact should be the same as in the past, mainly the small and medium-sized enterprises that produce medium and low-end products, while the domestic ones I’m afraid the manufacturers will bear the brunt of it, and there may be a new wave of shuffling.
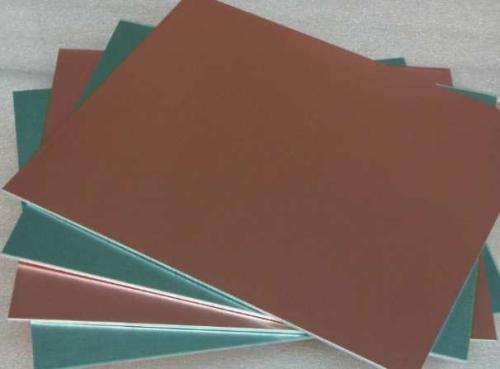
According to relevant supply chain operators, the proportion of raw material price in the cost of different PCB product types is quite different. Generally, for example, high-end PCB board, HDI or higher-end SLP, IC board, etc., a large part of the cost structure of these technology-oriented products will come from the depreciation of high-end equipment, and the proportion of raw material cost will be compressed, but if it is production technology For the lower middle and low-end rigid pcb, the proportion of raw material cost is naturally higher, which is why the middle and low-end products are generally regarded as the number one victim of this wave of price rise.
In addition to the different PCB products, the actual market situation will also make the impact of cost increase different. For example, for
HDI PCB, which is facing a sharp shortage of production capacity, it is not easy for CCL to really increase the price. The main reason is that the time for pulling goods is tight. In order to ensure a stable supply of CCL products, PCB factories have already negotiated long-term supply orders.Therefore, even if CCL companies want to cooperate with the upstream material price changes to increase the price in a short time, it is not easy to achieve.
Of course, the key factor for most of the suppliers to negotiate is the large scale of the suppliers. On the other hand, when facing the large scale of the suppliers, the suppliers have to face the large price. On the other hand, the key factor is the large scale of the suppliers Leading PCB manufacturers have to wait until the last minute to persuade them to accept the new price.
Under the “strong” of large factories, small and medium-sized manufacturers with medium and low-end products have no control over the price of raw materials. Therefore, the small and medium-sized enterprises with weak negotiation ability will probably suffer the most. Due to the lack of production scale and the fact that many small and medium-sized enterprises producing medium and low-end products are facing the Red Sea in the end market, if they can not grab enough raw materials to ship, they will become losers.
Large
PCB manufacturers have disclosed that they have recently received upstream CCL suppliers who hope to increase the price demand. However, the company has not made relevant decisions. The main reason for this margin is that the company’s own technology and scale belong to the leading group, and they have an advantage in price negotiation. However, small and medium-sized enterprises can only “bear the adversity” and many PCB suppliers can provide such a margin Chain operators believe that this will further accelerate the finishing speed of domestic low-end
custom PCB manufacturing lines.